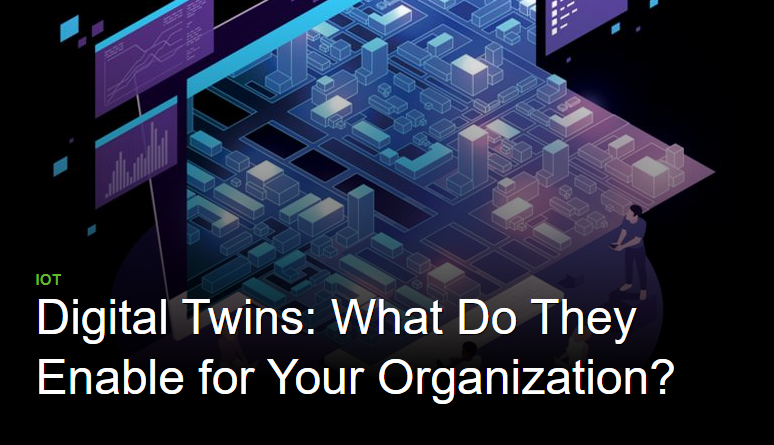
You’ve heard the phrase, digital twin. But what is a digital twin really for? Chris Lee, Customer Success Manager, Falkonry explains the trend behind the technology and for some important ideas about taking advantage of one.
What is a digital twin? There are many definitions (see sidebar), but they have much in common.
Digital twins…
-
- are digital representations of a physical system.
- take data from the real-world system they are twins to.
- reflect current and potential future states of the system.
- use insights from the data to understand the system and help achieve some business outcome.
More important than what a digital twin is, however, is what a digital twin is for. It’s more important to focus on what it enables than on how it is formally defined.
What Does a Digital Twin Enable?
By connecting data with models of system behavior and exposing them in an easily accessible way, a digital twin enables anyone in any business function to understand the current state of assets (or processes) so that they can do their job more effectively. That’s an almost unusably broad statement. To make it actionable, it helps to frame the idea in terms of the product life cycle (PLC). That is all the things that have to be done to design, test, build, support (and eventually retire) a product. This includes design engineering, manufacturing engineering, manufacturing operations, quality assurance, internal and customer training, sales, accounting, procurement, maintenance/field service and dozens of other roles that make an enterprise function. Enumerating all the different ways companies organize themselves to deliver their product and listing all of the tasks that each function performs would take many more words than anyone wants to read in an article like this, so I won’t try. Instead, let’s zoom in to one possibility to illustrate the larger idea.
Let’s say I’m the maintenance director at a plant that is firmly in the volume production phase of making Widget 3.14. This year’s objectives from the plant manager include an overall increase in output by 10%. A fraction of that objective will be achieved by increasing the availability of the widget oven. For this objective, a digital twin of the oven might incorporate real-time sensor data generated by the oven and a predictive failure model, which outputs a remaining useful life (RUL) to the Enterprise Asset Management (EAM) system. The EAM would use the RUL and other maintenance schedules to choose an optimal time to service the oven. The time chosen would maximize availability by juggling schedules to avoid unscheduled downtime due to early failures across all of the widget ovens in the line.
Another fraction of the output gain might come from minimizing the time to requalify the oven for production after maintenance. In this case, a different digital twin of the oven might take data from a special post-service test run of the equipment and use a multivariate machine learning model to compare the test run result to known “good” post-maintenance states. This might speed the verification process by eliminating time-consuming test runs and the associated time waiting for lab results to validate widget quality metrics.
Finally, a fraction of the objective may be achieved through a continuous improvement element in which a third widget oven digital twin collects operational data and applies anomaly detection models to identify novel patterns of operation. Instead of spending time extracting and puzzling over events from 6 months or a year ago to train AI models, by following an “Intelligence-first” approach, the equipment’s operations team would immediately start learning. This would include reviewing the digital twin reports on a daily basis and directing their attention to the current behaviors, which are important for identifying additional service or process improvements.
Of course, if my role were manufacturing quality assurance, my interest in digital twins might steer towards 3D design drawings, bills of material, performance specifications, and sensor feeds to create the right test and verification plans. If my role were in procurement, my interest in digital twins could be aimed at throughput and predictive quality models paired with Enterprise Resource Planning (ERP) forecasts, fed with real-time throughput and sensor data. Together this procurement digital twin of the widget oven could estimate the number of input materials required to maintain the target production level.
What is a digital twin? Because there are so many business goals and those goals look very different depending on your role, digital twins, in their particulars, get really complicated really fast. So rather than trying to get to a more precise definition, think about Dr. Grieves’ words: “CFOs don’t care about definitions. They care about the value for the investment.” Digital twins are there to help you achieve a business goal. Work from your specific goals, as the story above shows, and the definition of what your digital twin should be will flow more easily.